Regular inspections often reveal the need for prompt stretch wrap machine repair before equipment failure.
Regular inspections often reveal the need for prompt stretch wrap machine repair before equipment failure.
Blog Article
A Comprehensive Strategy to Dealing With Stretch Wrap Machine Repair Service Obstacles
You understand that stretch cover devices are crucial for maintaining effectiveness in product packaging operations. Concerns can emerge that interrupt performance. What are the best techniques to ensure your equipments run smoothly?
Recognizing Common Stretch Wrap Machine Issues
When you depend on stretch wrap makers for effective product packaging, it's important to acknowledge typical concerns that can disrupt operations - stretch wrap machine repair. One widespread trouble is irregular stress, which can bring about poor wrapping and jeopardized tons security. If you see the film isn't adhering properly, look for worn-out rollers or incorrect setups
One more concern you might face is film damage, frequently created by incorrect film type or device malfunctions. Routinely examine the equipment for indicators of wear and tear to avoid this.
Furthermore, watch on film accumulation or jams, which can halt manufacturing. Often, this occurs because of misalignment or debris in the machine.
Lastly, improper sealing can result in tons splitting up during transit. Make sure your machine is adjusted correctly to preserve the honesty of your packages. By remaining watchful and addressing these problems without delay, you can help with smoother procedures.
The Importance of Routine Preventive Maintenance
Normal precautionary upkeep is essential for maintaining your stretch cover machine running smoothly and effectively. By routinely inspecting and servicing your equipment, you can identify potential problems prior to they escalate into expensive fixings. This proactive method not only expands the lifespan of your maker but also ensures that it operates at peak efficiency.
You must set up normal inspections to tidy, oil, and change used parts. Maintaining your equipment adjusted helps keep perfect wrapping high quality, minimizes waste, and boosts productivity. Additionally, recording upkeep tasks creates a trustworthy background that can notify future choices.
Do not neglect the value of training your staff on maintenance ideal practices. When every person understands exactly how to care for the equipment, you minimize the danger of driver error causing failures. In short, committing to routine preventative maintenance is a clever investment that settles in lowered downtime and boosted performance in your operations.
Troubleshooting Methods for Quick Repair Works
Reliable troubleshooting methods can substantially lower downtime when your stretch wrap maker comes across issues. Beginning by recognizing the signs and symptoms. Is the maker not covering effectively or is it making uncommon noises? As soon as you have actually determined the trouble, refer to the operator's handbook for advice on common concerns and services.
Next, inspect the device's setups and controls; occasionally, a basic adjustment can resolve the concern. Examine the film tension and alignment, as incorrect configuration can lead to covering failures. Do not ignore electric links; loose or damaged cables can interrupt performance.
If you're still facing challenges, take into consideration running diagnostic examinations if your device has that ability. Document each action you take, as this can help in future troubleshooting and repair services. Finally, don't hesitate to speak with a technician if you can't fix the problem swiftly. Effective troubleshooting keeps your procedures running efficiently and decreases pricey delays.
Educating Operators for Effective Maker Use
To assure your stretch cover device operates at peak efficiency, proper training for drivers is vital. When operators recognize the device's functionalities, they can maximize its possible and minimize downtime.
Motivate them to exercise under supervision, attending to any concerns or concerns they may have. Frequently set up correspondence course can maintain their skills sharp and aid them adapt to any type of updates or adjustments in technology.
Furthermore, impart a society of accountability by equipping drivers to report concerns or recommend improvements. This positive technique not just enhances their confidence yet additionally adds to the total effectiveness of your operations. With trained drivers, you'll see less mistakes and enhanced efficiency, ensuring your stretch wrap machine stays a useful asset.
Constructing a Solid Interaction Channel In Between Teams
Trained drivers can just carry out at their ideal when there's a strong interaction network between teams. Efficient communication eliminates misunderstandings and guarantees everyone's on the same web page regarding machine operations and repair needs. Urge normal check-ins and conferences to go over problems, share insights, and address issues.
Using innovation, like messaging apps or collaborative systems, can boost real-time interaction, making it less complicated to report troubles and share updates promptly. Designating clear functions and obligations fosters accountability, permitting group participants to connect to the appropriate individual when problems develop.
Furthermore, creating an open setting where every person feels comfortable sharing responses can cause innovative remedies. By focusing on communication, you're not simply enhancing machine efficiency; you're likewise building a natural group that interacts flawlessly. This helpful site collective spirit ultimately leads to quicker repair services and decreased downtime, benefiting the entire procedure.
Buying Top Quality Replacement Parts
When it comes to preserving your stretch cover devices, buying quality replacement components is necessary for making sure reliable efficiency and decreasing downtime. Affordable choices may seem alluring, but they commonly lead to more substantial issues down the line, costing you much more out of commission and lost efficiency. By choosing top notch parts, you're not just taking care of a trouble; you're enhancing the overall effectiveness of your tools.
Additionally, quality parts are typically manufactured to stricter criteria, which implies they'll fit much better and work more dependably. This minimizes the probability of unanticipated failures, allowing your operations to run smoothly. Furthermore, credible distributors often provide warranties, giving you peace of mind in your financial investment.
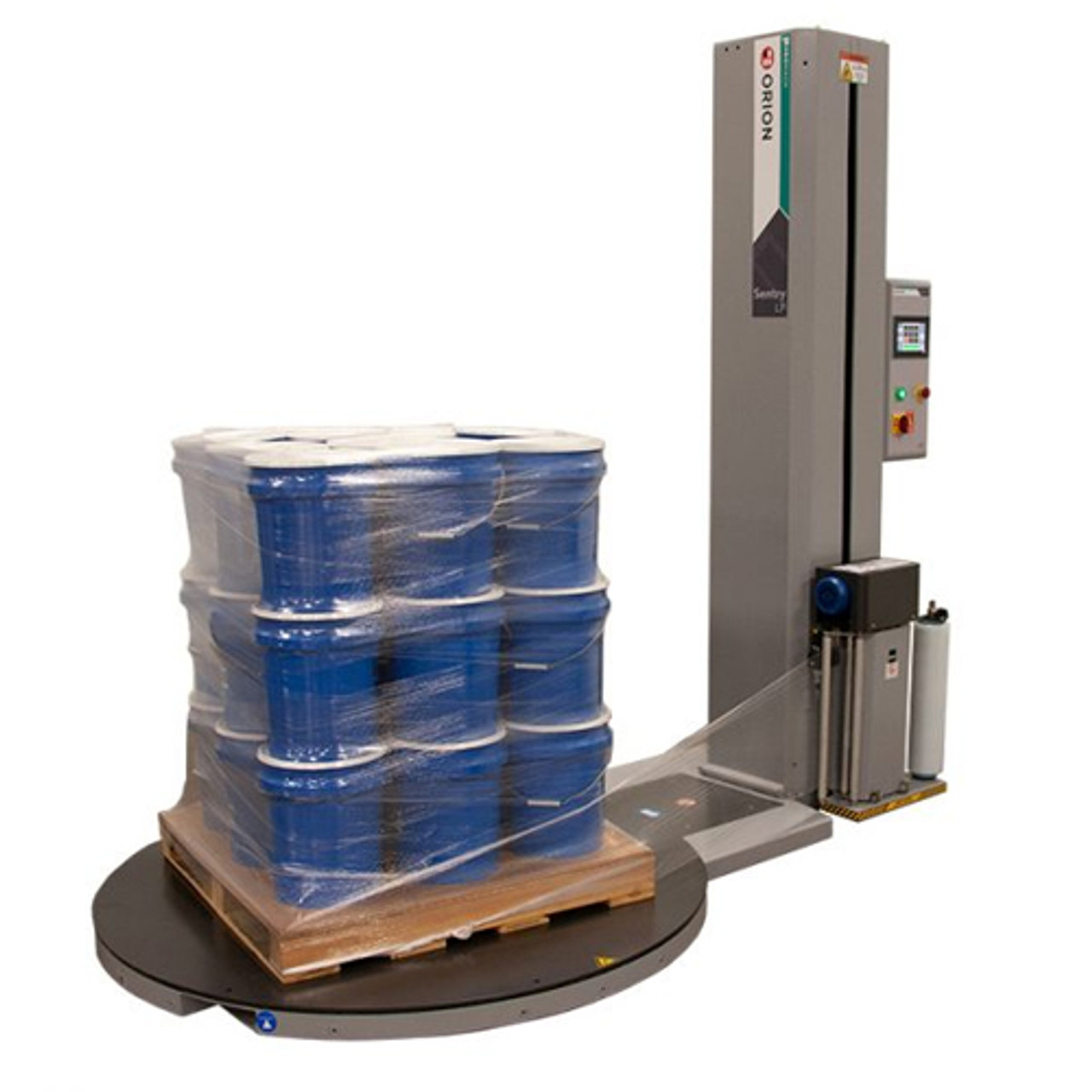
Analyzing Performance Information for Continuous Enhancement
To boost your stretch wrap equipment's performance, you need effective information collection methods. By reviewing performance metrics, you can determine areas for enhancement and increase efficiency. Recognizing these opportunities not just enhances operations however also lowers downtime and repair expenses.
Data Collection Techniques

Efficiency Metrics Analysis
While examining efficiency metrics, it's vital to focus on particular information points that straight impact your stretch wrap equipment's efficiency. Begin by tracking cycle times, as they disclose exactly how quickly your device operates under typical conditions. This continuous evaluation assists enhance performance, decrease expenses, and eventually improve your equipment's durability, leading to a more effective wrapping procedure in general.
Recognizing Improvement Opportunities
As you examine efficiency information, you can uncover important renovation possibilities that enhance your stretch wrap machine's efficiency. Look for patterns in downtime, cycle times, and cover top quality. If regular break downs associate with details operating problems, you can change processes to reduce these problems.
Often Asked Concerns
Exactly How Can I Tell if My Device Needs a Repair or Just Maintenance?
To inform if your maker needs repair or just maintenance, pay attention for uncommon sounds, check for inconsistent performance, and inspect for noticeable wear. If issues continue after upkeep, it's likely time for a repair service.
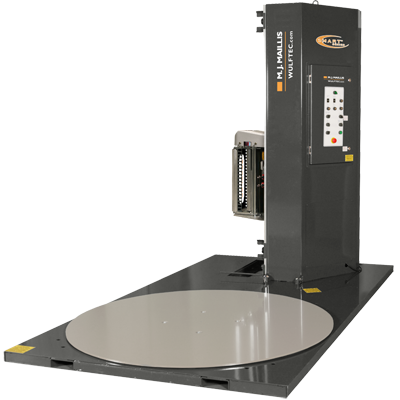
What Is the Typical Life Expectancy of a Stretch Wrap Device?
The average lifespan of a stretch wrap machine is normally 5 to 10 years, depending on use and upkeep. Routine care can prolong its life, so keep an eye on performance and address issues promptly.
Are There Specific Brand Names Recognized for Better Dependability?
Yes, some brands are known for their reliability. You'll locate that firms like Signode and Lantech usually get positive reviews - stretch wrap machine repair. Looking into customer comments can help you pick a trustworthy stretch wrap machine for your demands
What Are the Indications of Poor Driver Training?
If you observe frequent mistakes, inconsistent covering, or security events, those are indicators of bad driver training. Lack of recognizing regarding machine features or failure to comply with protocols can substantially affect performance and security.
Just How Can I Find a Professional Specialist for Services?
To find a certified technician for repair services, request for suggestions from market peers, examine online evaluations, and validate certifications. You may likewise take into consideration getting in touch with regional tools suppliers who often have trusted professionals on hand.
Conclusion
To sum up, dealing with stretch wrap equipment repair service difficulties requires an aggressive technique. Don't neglect the value of strong interaction between groups and constant like it evaluation of equipment outcome.
Report this page